Filtration System for Melt Polymer filtration
Melt Polymer Filtration System
A melt polymer filtration system is essential in many applications where polymers are processed or used, such as in the production of PET/PA/PP polymer industry, pre-polymerizaton, final polymerization, filament yarn, polyester staple fiber spinning, BOPET/BOPP films, or membranes. This system helps remove impurities, contaminants, and viscosity-affecting particles from the molten polymer, ensuring the quality and consistency of the final product.
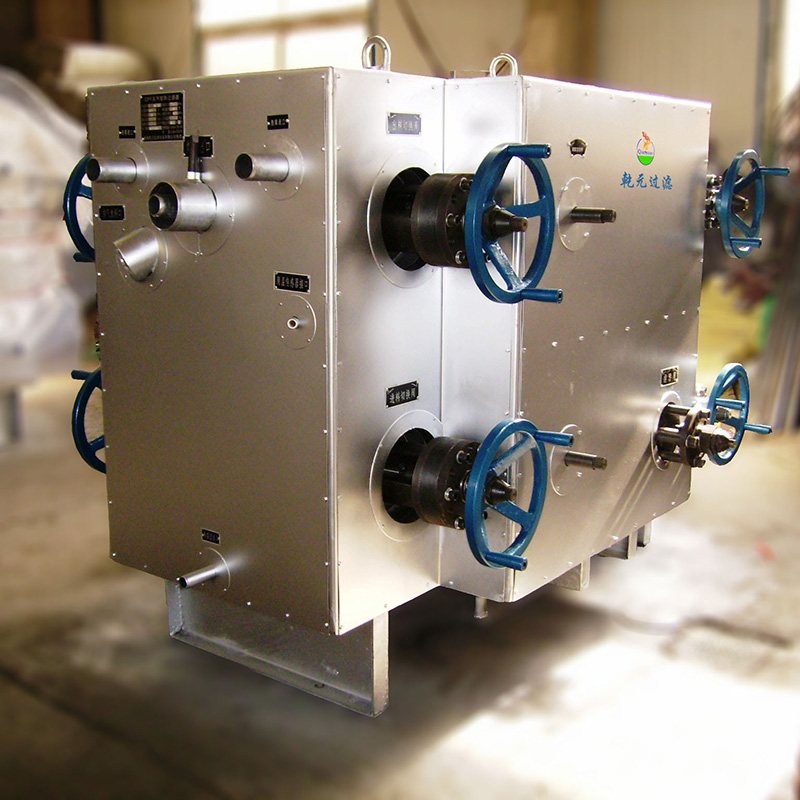
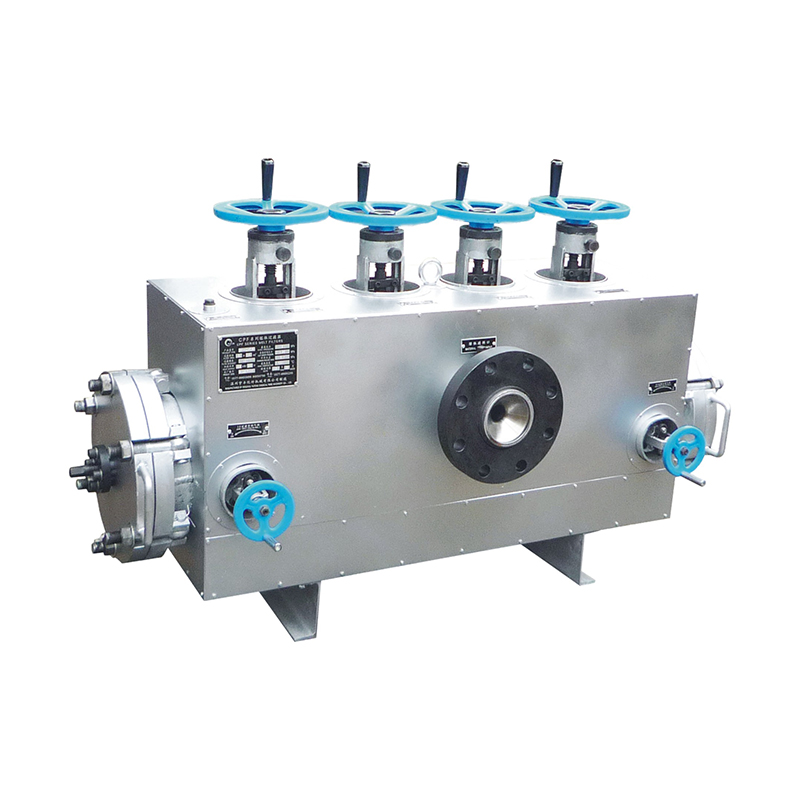
In order to improve the quality of the melt polymer and prolong the service life of the spin pack components, a continuous melt filter (CPF) is installed on the main melt pipe. It can remove mechanical impurities particles with a diameter greater than 20-15μm in the melt, and also has the function of homogenizing the melt. Generally the filtration system consists of two filter chambers, and the three-way valves are connected to the melt pipeline. The three-way valves can be switched periodically to alternate the use of the filter chambers to ensure continuous filtration. The housing of the filter chamber is cast in one piece with stainless steel. The large-area filter is composed of multiple pleated candle filter elements. The candle filter element is supported by a core cylinder with holes, and the outer layer is equipped with a single or multi-layer metal mesh or sintered metal powder disc or multi-layers metal mesh & sintered fiber or sintered metal wire mesh, etc.. in different filtration rate which is based on the requirements of final products.
In general there are different types of filtration system, such as Horizontal continuous filtration system, vertical continuous filtration system. For example, during the PET chips spinning process, the vertical candle-type filter type is commonly proposed, which is with a filtration area of 0.5㎡ per candle core. There are commonly used configurations of 2, 3, or 4 candle cores, corresponding to filtration areas of 1, 1.5, or 2㎡, and the corresponding melt filtration capacities are 150, 225, 300 kg/h. The vertical filtration system has a larger size and more complex operation, but it has many advantages from a process perspective: (1) It has a large thermal capacity, small melt temperature variation, and no dead zones when the material flows. (2) The insulation jacket structure is reasonable, and the temperature is uniform. (3) It is convenient to lift the filter core when switching the filter.
The pressure difference before and after the newly used filter is low. As the usage time increases, the filtering medium holes gradually become blocked. When the pressure difference reaches the setting value, e.g, such as for PET chips spinning, generally the figure is about 5-7MPa, the filter chamber must be switched. When the allowed pressure difference is exceeded, the filter mesh may be twisted, the mesh size increases, and the filtration precision decreases until the filter medium is ruptured. The switched filter core must be cleaned before reuse. The clarity of the effect is best determined by the "bubble test" experiment, but it can also be judged based on the pressure difference before and after the newly switched filter. Generally, when the candle filter has been ruptured or cleaned 10-20 times, it should no longer be used.
For example, for Barmag NSF series filters, they are heated by Biphenyl steam in the jacket, but the temperature of the heat transfer fluid should not exceed 319℃, and the maximum Biphenyl steam pressure is 0.25MPa. The maximum design pressure of the filter chamber is 25MPa. The maximum allowed pressure difference before and after the filter is 10MPa.
Technical Parameters
Model | L | B | H | H1 | H2 | FIX(H3) | Inlet&Outlet DN(Φ/) | Filter Area(m2) | Applicable Screw Bar(Φ/) | Designed Flow Rate(kg/h) | Filter Housing | Filter Element | Total Weight(kg) |
PF2T-0.5B | 900 | 1050 | 1350 | As customer's Site | 2200 | 22 | 2x0.5 | 65 | 40-80 | Φ158x565 | Φ35x425x4 | 660 | |
PF2T-1.05B | 900 | 1050 | 1350 | 2200 | 30 | 2x1.05 | 90 | 100-180 | Φ172x600 | Φ35x425x7 | 690 | ||
PF2T-1.26B | 900 | 1050 | 1390 | 2240 | 30 | 2x1.26 | 105 | 150-220 | Φ178x640 | Φ35x485x7 | 770 | ||
PF2T-1.8B | 950 | 1140 | 1390 | 2240 | 40 | 2x1.8 | 120 | 220-320 | Φ235x620 | Φ35x425x12 | 980 | ||
PF2T-1.95B | 950 | 1140 | 1390 | 2240 | 40 | 2x1.95 | 130 | 250-350 | Φ235x620 | Φ35x425x13 | 990 | ||
PF2T-2.34B | 1030 | 1200 | 1430 | 2330 | 40 | 2x2.34 | 135 | 330-420 | Φ235x690 | Φ35x485x13 | 1290 | ||
PF2T-2.7B | 1150 | 1200 | 1440 | 2350 | 50 | 2x2.7 | 150 | 400-500 | Φ260x690 | Φ35x485x15 | 1320 | ||
PF2T-3.5B | 1150 | 1250 | 1440 | 2350 | 50 | 2x3.5 | 160 | 500-650 | Φ285x695 | Φ35x485x19 | 1450 | ||
PF2T-4.0B | 1150 | 1250 | 1500 | 2400 | 50 | 2x4.0 | 170 | 600-750 | Φ285x735 | Φ35x525x19 | 1500 | ||
PF2T-4.5B | 1150 | 1250 | 1550 | 2400 | 50 | 2x4.5 | 180 | 650-900 | Φ285x785 | Φ35x575x19 | 1550 | ||
PF2T-5.5B | 1200 | 1300 | 1500 | 2350 | 50 | 2x5.5 | 190 | 800-1000 | Φ350x755 | Φ50x500x15 | 1650 |